The Power of Ultrasonic Imaging with Acoustic Cameras in Industrial Maintenance and Asset Management
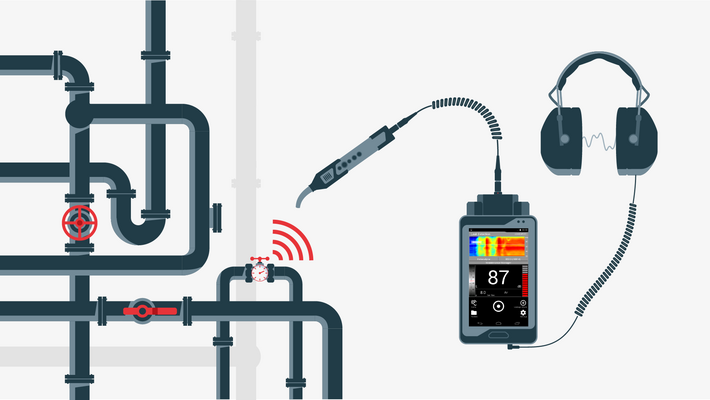
Ultrasonic imaging is a cutting-edge technology that uses high-frequency sound waves to detect and visualize issues in various industrial systems. Acoustic cameras, which capture and convert these ultrasonic signals into visual images, leverage this technology to revolutionize the detection and maintenance of equipment problems. The advanced approach allows for rapid identification and precise localization of compressed air leaks, specialized gas leaks, mechanical faults, and electrical partial discharges, transforming industrial maintenance and asset management.
1. Precise Detection of Compressed Air Leaks
Compressed air systems are essential in many industrial operations but are often prone to leaks that can waste energy and increase operational costs. An acoustic camera with an ultrasonic compressed air leak detector, such as the FLIR Si-Series, enables quick identification of these leaks by visually pinpointing the leak locations accurately.
The technology allows maintenance teams to perform prompt repairs, improving system efficiency and reducing energy wastage. Also, instruments with a customized software plugin can estimate leak volume and cost savings, further supporting efficient and cost-effective maintenance practices.
Unlike most gas leak detection methods, ultrasonic cameras can precisely detect leak location by visualizing ultrasonic sound waves emitted from leaks, making it highly precise. Also, ultrasonic imaging technology in acoustic cameras can detect these leaks early, ensuring safety, reducing waste, and protecting personnel and the environment from potential hazards.
2. Rapid and Automatic Detection of Mechanical Faults
Mechanical faults in equipment such as motors, pumps, and bearings can lead to costly breakdowns if not addressed promptly. Ultrasonic imaging captures ultrasonic signals that faulty components emit, allowing for early intervention and maintenance, extending the machinery’s lifespan, and preventing costly failures.
Quality and advanced acoustic cameras offer rapid fault detection while automatically classifying faults, indicating severity, and recommending actions.A special software plugin for specific acoustic cameras unlocks automatic fault classification. The integration supports efficient maintenance practices by combining acoustic and thermal imaging in comprehensive reports, enabling maintenance teams to quickly identify issues and take corrective actions before minor faults escalate into significant problems.
3. Enhanced Detection of Electrical Partial Discharges
High-voltage electrical systems such as power transmission lines and transformers can suffer from partial discharges (PD) that compromise insulation and pose serious risks. PD is one of the earliest signs of an emerging fault in electrical systems. Advanced acoustic cameras leverage ultrasonic imaging to identify the signs of PD, offering the best chance of mitigating problems before they occur.
The advanced PD measurement and monitoring solutions enable maintenance teams to take preventative measures before severe damage occurs, ensuring the reliability and safety of electrical infrastructure.
Ultrasonic imaging works by detecting the high-frequency sound waves partial discharges emit. Modern and advanced acoustic camera models use artificial intelligence to classify the specific type of partial discharge—surface discharge, floating discharge, or corona—allowing easy and precise identification and targeted repairs.
4. Reduced Downtime: Enhanced Accuracy, Speed and Efficiency
Acoustic cameras can enhance industrial operations through proactive maintenance by enabling fast routine inspections and accurate identification of emerging issues. These cameras provide precision in repairs by swiftly pinpointing potential faults such as compressed air leaks, mechanical failures, and electrical partial discharges. The proactive approach allows maintenance teams to take immediate corrective actions, minimizing downtime and optimizing operational efficiency.
Industries can achieve higher reliability and reduced operational disruptions by integrating acoustic imaging into regular maintenance practices. Accurate and timely identification ofequipment issues ensures targeted and effective repairs, extending equipment lifespan and enhancing overall productivity. Thus, acoustic cameras are crucial in ensuring smooth and efficient industrial operations through proactive and responsive maintenance strategies.
5. Non-Destructive Testing
Ultrasonic imaging empowers acoustic cameras to see beyond barriers to help inspect and detect issues non-destructively. Unlike traditional methods requiringtechnicians to dismantlecomponents or take equipment offline, acoustic cameras can assess machinery while it remains operational.
By capturing and analyzing ultrasonic signals emitted by equipment at multiple points, these cameras provide a comprehensive view of potential issues without physically interfering with the machinery. The unique capability allows maintenance teams to proactively identify and address emerging problems such as carbon dioxide leaks in open cast mines, mechanical wear of industrial cutting tools, and electrical anomalies before they lead to costly downtime.
The non-invasive nature of acoustic cameras using ultrasonic imaging saves time and minimizes disruption to production processes. These cameras are invaluable for ensuring equipment reliability and optimizing operational efficiency in industrial environments.
6. Increases Accessibility: Hard to Reach and Hazardous Areas
Ultrasonic imaging with acoustic cameras significantly improves accessibility and efficiency in inspecting various hard-to-reach and hazardous areas in industrial settings. Such applications include the following;
- Inspecting Insulated Pipes and Vessels: Traditional methods involve removing insulation, which is time-consuming and disrupts operations. Acoustic cameras, however, can penetrate insulation to identify leaks or other issues without needingthe removal of the insulator.
- Detecting Faults in Confined Spaces- Tanks and Boilers: These spaces pose challenges for manual inspection due to safety concerns. Acoustic cameras enable inspection from outside these spaces, detecting leaks and electrical faults or assessing equipment conditions internally, enhancing safety and efficiency.
- Inspecting Underground Infrastructure: Inspecting underground infrastructure like buried pipes or cables traditionally involves excavation, which is costly and disruptive. Ultrasonic imaging offers a non-destructive alternative, allowing assessment without digging.
- In Machinery Operational Environments: In areas where machinery inspection is risky, acoustic cameras provide a safe distance inspection method for identifying issues like bearing wear or gear malfunctions without equipment shutdown.
- Inspecting Environments with High Temperatures or Toxic Materials: Inspecting hazardous zones, whether due to high temperatures or risk of exposure to toxic materials, deploying acoustic cameras from a distance helps to minimize human exposure, ensuring safety while efficiently assessing conditions.
Such ultrasonic imaging applications in acoustic cameras streamline inspection processes, offering quick, efficient assessments of large areas or complex equipment from safe distances, ideal for hard-to-reach and hazardous environments in industrial operations.
In conclusion, acoustic cameras leveraging ultrasonic imaging capabilities have transformed industrial inspections, enhancing speedy, accurate, and non-disruptive assessments while making inaccessible or hazardous areas accessible. These advancements allow for proactive maintenance, minimizing downtime, and optimizing operational efficiency across various industrial sectors.
However, choosing a reputable camera brand guarantees advanced technology integration, robust build quality, and reliable performance. Such a combination allows industries to enhance efficiency, reduce downtime, and maintain safety standards effectively, setting new benchmarks in maintenance and operational excellence.